Steel Inspection Specifications: 1.Inspection basis: GB700-88 carbon structural steel, GB699-88 high-quality carbon structural steel, supplier's standard.
2.Inspection ratio: one sample per batch.
3.Inspection items:
A. Check the material specifications, brand, manufacturer, finished product , mill certificate, etc.
B. Appearance quality: no cracks, inclusions and other defects visible to the naked eye.
C, size and quality: according to the supplier's enterprise standards and relevant national standards.
D. When in doubt about the material, send it to the relevant department for chemical analysis.
Outsourcing parts, fastener inspection specifications 1.Inspection basis: The external contract documents shall be in accordance with the acceptance standards stipulated in the contract. Fastening standard parts are in accordance with industry standards and enterprise standards.
2.Inspection proportion:
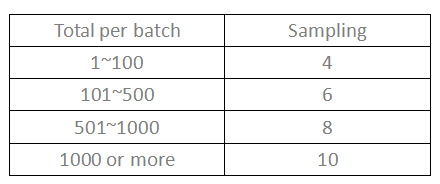
3.Inspection items:
A. Check the material specifications, brand, manufacturer, product wheat, warranty certificate, etc.
B. Appearance quality: no defects such as variegated spots and burrs visible to the naked eye.
C, size and quality: according to the supplier's enterprise standards and relevant national standards.
D. When in doubt about the material, send it to the relevant department for chemical analysis.
4.Quality judgment:
If the items in the B and C dimensions are unqualified, the inspection will be doubled. If the unqualified items are found, the whole batch will be disqualified.
The item D is unqualified or one unqualified is found in the random inspection. The batch of products shall be treated as unqualified.